Dallas Residents - Learn Lean Six Sigma’s History Here
Contact Us
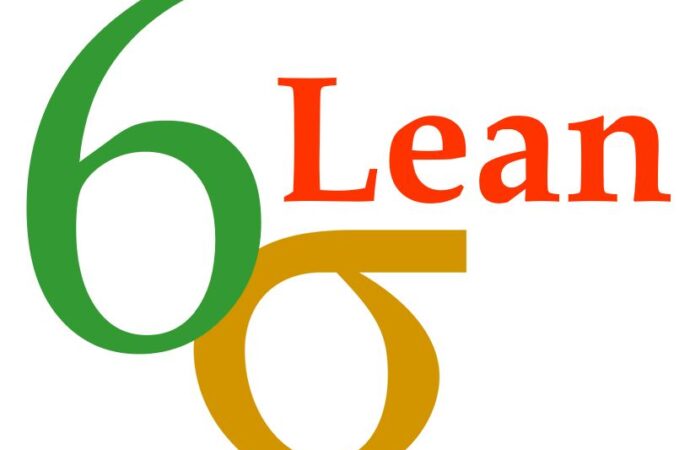
Lean Six Sigma is a growing methodology in more than manufacturing as professionals and students are noticing its benefits for processes and systems overall and not only for production. However, how is this methodology growing, and when did it start? At Lean Six Sigma Curriculum for Dallas High School Students of Texas, we worry about teaching those interested from the very inception and how the USA has gotten the best from this method.
Let’s first establish that Lean Six Sigma is a blend of Japanese management methods and principles that can later be traced back to the United States. Kaizen, which emphasizes cooperation and commitment as a means of continuous improvement, is the Japanese influence on the Lean Six Sigma method.
But the main aspect and principles of Kaizen that make LSS so valuable are: process, product, people, and environment. Kaizen is different from other methods in that it focuses on the idea of small, positive changes. It also eliminates unnecessary steps and processes, which saves time.
Now, how is a methodology that has its origins come from Japanese working in the USA?
It can be traced back to the USA, which was developed as a new method to compete with Japanese industries. LSS was founded in the 1980s to compete with Japan’s superior products and to adopt Japanese principles for better results due to the previous Kaizen ideology.
These principles were designed to reduce waste by taking non-value-adding measures and were adopted in large U.S. corporations in the 1990s. Although it has its “roots” in a foreign country, it is more about an adaptation to find a solution to compete with their products and services.
But, where does this leave Six Sigma in history and its current use in the USA?
Lean Six Sigma Origins & Introduction in the American Market
Although the idea of the methodology comes from Kaizen, its inception and how it is built come from two individual ones: Lean and Six Sigma.
This means it is required to understand the differences between Six Sigma and Lean, as they are two distinct elements that were combined and had aspects in common, but also basics and principles established by each one for the combined methodology we will be using.
Due to its structure and principles, first, Lean is often considered for customer satisfaction and reducing waste. People often refer to the origins of Lean when mentioning Toyota.
Toyota worked in its system as the “Toyota Production System” (TPS). John Krafcik, a researcher at MIT in 1987, was one of the people researching it and working on its development.
He was looking for a name to describe the TPS system. He wrote down the characteristics and differences between Toyota’s system and traditional mass production on a whiteboard. After his analysis and research, he concluded that the Toyota system needs less of everything to create value.
Lean Thinking was born quickly from this. It focuses on reducing waste and non-value-added activities. The Japanese influence is evident in Japan’s Kaizen principles.
Lean has its own foundations and principles. This includes understanding the customer and understanding the value stream and waste of each process. Value flow is influenced or completely based on Kaizen.
On the other hand, Six Sigma is an American-based organization with roots dating back to the 1980s. Motorola is the originator of Six Sigma. Motorola was a struggling competitor to foreign companies at the time, and its CEO Bob Galvin set a goal of tenfold improvement in five years.
This plan focused on global competitiveness and how he had to work around improvement, participative management, quality, and productivity. Six Sigma became the standard for all Motorola business processes within no time, and training was provided to every employee.
When taken together, Six Sigma and Lean both recognize that the process is what must change. Six Sigma is a great addition to the Lean approach as it complements what the other is missing and vice versa.
Thus, the Kaizen methodology remains Japanese, but the development of Lean and 6 Sigma comes from the USA itself to come up with the entire LSS ideology.
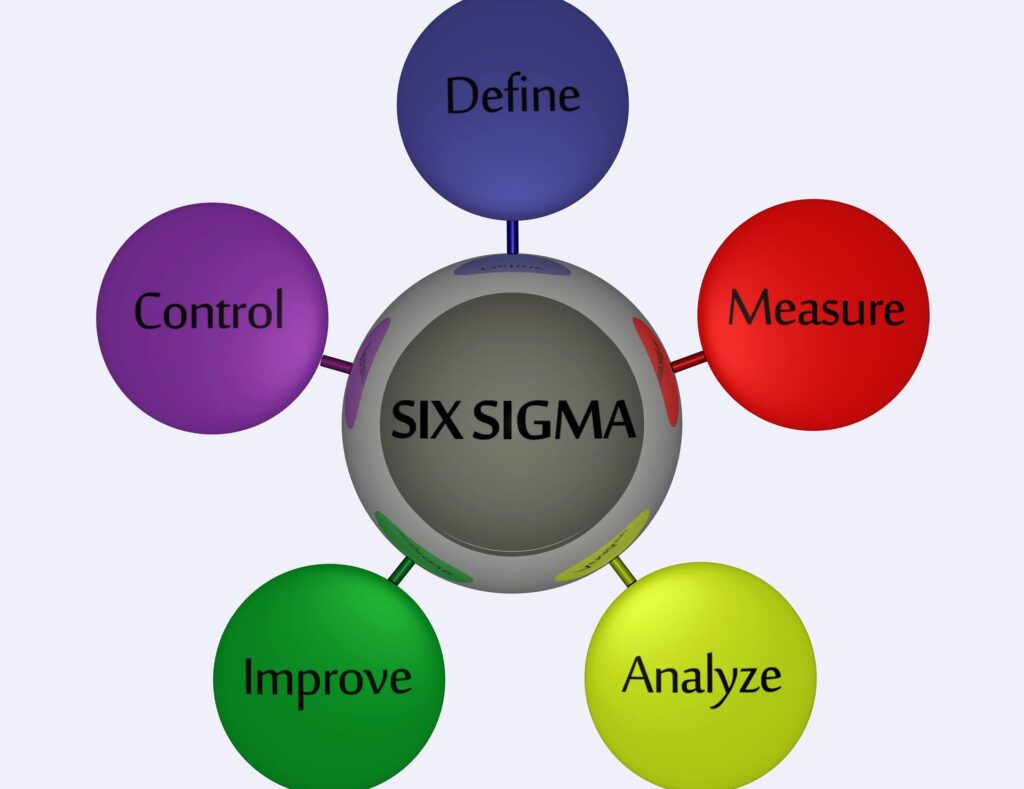
But How Is It Used?
LSS has been used in many ways throughout history. It is designed to increase productivity and efficiency and reduce waste.
It’s a good idea for people to understand the principles and solutions of Lean, Six Sigma, and Kaizen. This will help them see the benefits and drawbacks of the full methodology.
Lean allows workers and companies to understand customers better and prioritize their needs. However, they can still focus on the company’s value stream, processes, and value flow to achieve perfection.
Six Sigma is committed to excellence and a system that ensures more efficiency and clean processes. Continuous improvement and innovation are key goals of 6 Sigma.
Lean Six Sigma can be used for its many benefits to businesses, students, and professionals undergoing training. When working on it, they will be able to:
- Learn how to reduce waste.
- Increase efficiency.
- Reduce errors.
- Reduce legal risk for the company.
- Time management can be improved.
- Lower costs mean higher revenues and better salaries.
- Gain motivation.
- Innovation and leadership are fundamentals.
All this follows the DMAIC structure of 6 Sigma and the principles around each method involved.
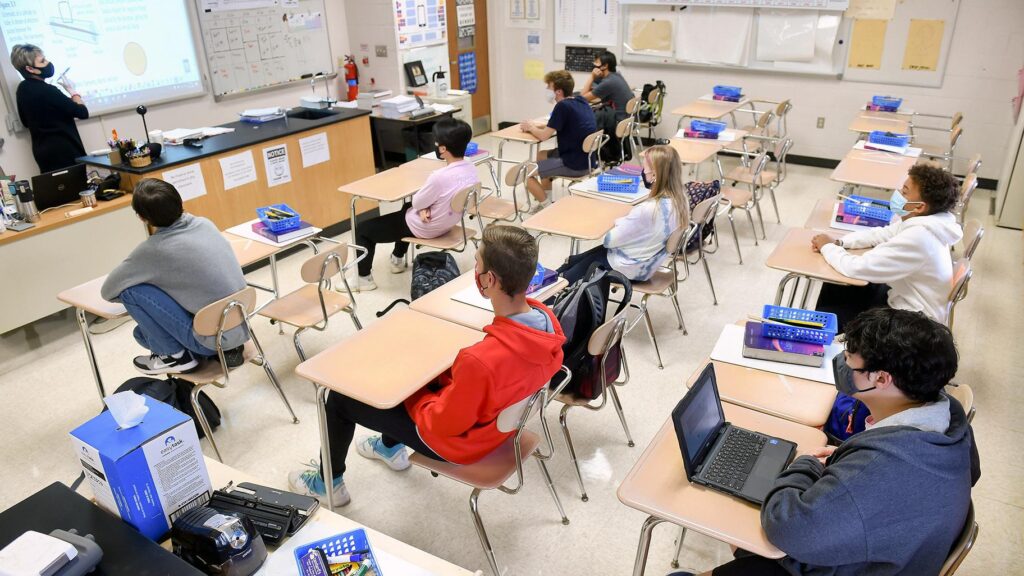
Be Part of History!
Contact our Lean Six Sigma Curriculum Pros of Dallas team in order to access all the training and certifications available. You, your students, or workers will be able to be part of the group of people who know how to work around problem-solving and continuous improvement.
We are experts in the history of Lean Six Sigma and how it works. We can also teach high school students, college students, business professionals, and entire companies how to implement LSS into their lives, so it isn’t work-focused only.
We want to make sure you have all the benefits and that you are a valuable resource in any place or company you choose to work for and add more value to American generations.